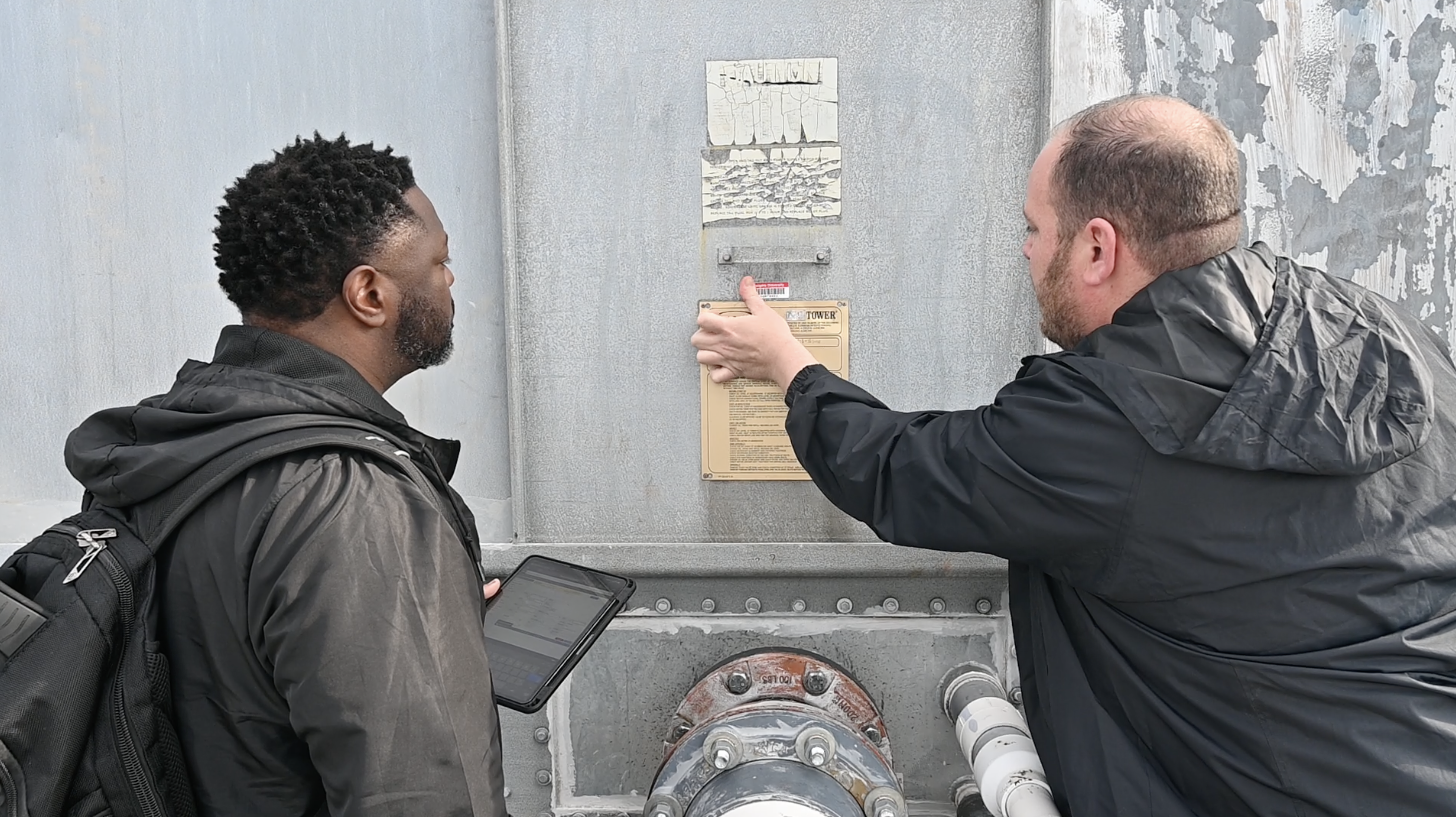
From Rutgers oldest buildings to its newest, upkeep is critical to a building’s lifecycle. The Facilities Condition Analysis (FCA) group spends its days building a dynamic information database to support operational requirements and strategic planning goals of the university. This group is the central resource for all building asset and assessment documentation, setting the standards and procedures for the use of the asset database, inventorying the mechanical parts in each of our buildings, assessing building conditions, and logging the information into a single system. This ultimately gives the building mechanics an accurate record of what is in the building and how it should be maintained while providing valuable insight into future university wide strategic needs.
“One of our many tasks is to support a strong maintenance program. We accomplish that by building a solid asset database and sustaining it every day,” said Jelani Dukes, Facilities Coordinator.
Rutgers has buildings dating back to the 1800s through to the present day. As buildings age, assets are sometimes replaced at set intervals or as needed prior to the end of their lifecycle. This is called asset renewal. Sometimes, however, asset renewal is deferred due to lack of money, insufficient manpower, material supply chain issues, etc. This is called deferred maintenance. Rutgers, like many universities, has an extensive deferred maintenance backlog. This can lead to many issues such as equipment break down, which in turn results in emergency maintenance rather than preventive maintenance. The FCA group is instrumental in helping to address these issues, bringing order to the process of asset management.
“Our work supports the overall building value and building costs,” explained Dukes, who along with another Facilities Coordinator, Thomas Farley, spend their days in and out of buildings assessing the equipment. “If you have 20 exhaust fans in a building, how do you know which one is due for maintenance at any given time,” said Farley. “We locate the asset and put it on a maintenance schedule. We create a process that plays an integral part in a positive daily experience for the university community,” he added.
Currently there are over 50,000 assets in the FCA database. According to James Boswell, FCA’s Assistant Director, while his team has tagged, inventoried, and set up a maintenance schedule for many Rutgers buildings, there are many more assets that have not yet been recorded. “The team is out in the field everyday covering a lot of ground. I’m very strategic when scheduling so I can maximize their time. Eventually, we will get to every asset in every building.”
The key to making that happen is developing a strong, close working relationship with building project managers, Area Managers, Planner Estimators, and mechanics. It also involves the use of helpful technology like BIM360. When a building is renovated or built brand new, it helps to get an inventory list of everything that was put into that building or renovated space,” Boswell explained. “We use BIM360 to streamline this aspect of our work. We extract the equipment schedule directly from the drawings and reference it when on site. It’s a map to guide us and ensure that we are as accurate as possible when entering information into the asset database.”
Communication is also key and the FCA group is currently reaching out to mechanical maintenance shops with their “Road Show” presentation. Connecting with mechanics is a central part of the agenda and plenty of time is spent showing how the notes provided on preventive maintenance work orders contribute to the asset database. There is also a hands-on interactive portion that builds confidence and reinforces the importance of their role in the process.
Whether they are performing field work, setting up schedules, interacting with the latest technology, or sharing methodology with colleagues, the FCA group is doing their part to ensure Rutgers buildings enjoy a long and well maintained lifecycle.